
Class F Control House and Crane Modernization
Class F Control House and Crane Modernization
This case study outlines the upgrade of an existing 55-ton capacity Class F magnet service overhead crane.
Because of the severe service under which the crane operated and the age of the crane, the following major issues were addressed:
- Replace the entire trolley and hoists
- Install complete Magnetek controls with AC Regen control
- Complete new festoon system
There were a host of problems on the trolley and with limited time during shutdowns we felt replacing the trolley and hoist complete was more time and cost effective.
The existing controls were for the most part based on older static stepless wound rotor motor controls. Rather than completely replace the control house, we proposed stripping the control house and installing the new Magnetek controls on custom pre-engineered back panels that were designed to fit in the existing control house enclosure.
The goals for this project included:
- Zero injuries or accidents during the work period
- Replace all controls for the crane
- Replace wound rotor motors with invertor duty squirrel cage motors
- Replace all brakes with Thruster brakes
- Replace the entire festoon
- Provide PLC based HMI oversight of the crane and crane operations for the operator, and expanded HMI capabilities for maintenance.
- Leave the crane with a higher operational time, with lower cost of ownership controls and devices
The pictures below show some of the project in process.
The Control House controls as were existing.
Original Crane Control House.
Picture of the original trolley/hoists just prior to removal.
Engineered Lifting Systems Field Engineer surveying the old festoon.
Here is a picture of the replacement Ace World Companies trolley with main and auxiliary hoist still at Ace World’s shop.
The control house was gutted getting ready for the new controls.
Magnetek build the panel modules not only to fit the control house enclosure, but also performed a complete testing prior to shipment.
Magnetek modules were lifted into place in the original control house.
Magnetek panel modules were placed in stands for ease of installation.
New Festoon system installed and almost ready for operation.
This is a good picture showing the scope of installation.
Control House during installation.
Control House with final programming on the PLC and HMI.
The modernized crane now gives the customer a high percentage of production time at a fraction of the cost of a new crane.
Magnetek controls and Ace World Companies integrated together on this project have provided huge benefits for the customer. Careful planning and engineering made the installation (almost) seamless.
If you have an old crane and want to investigate a modernization instead of a replacement, please call Engineered Lifting Systems!
Recent news posts
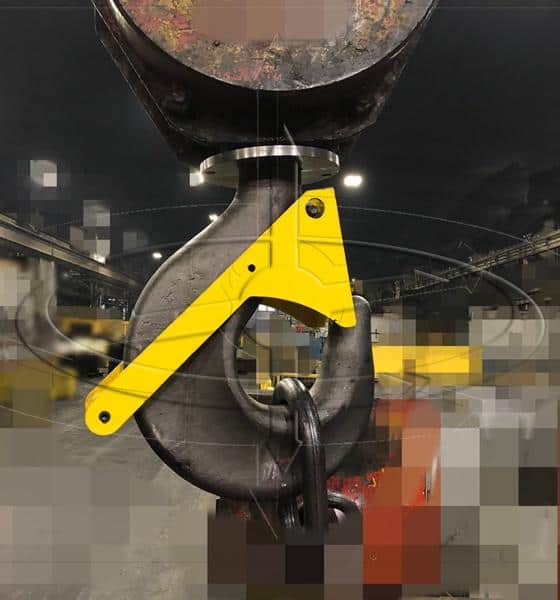
Gravity Latch with Rotation Lock
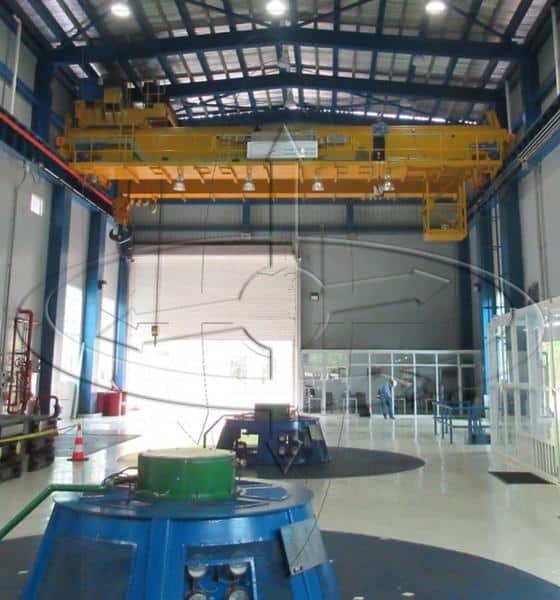
Magnetek Series 3 Drives Using “Motor 2” Option
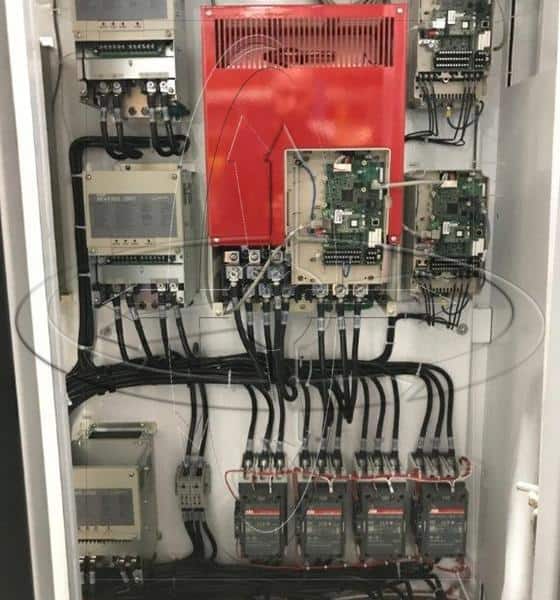
Magnetek Brake Circuit Fusing
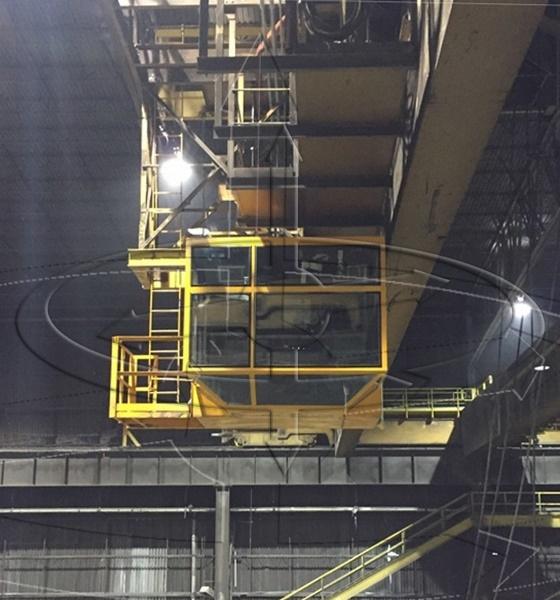
Crane Cab Replacement Improves Function
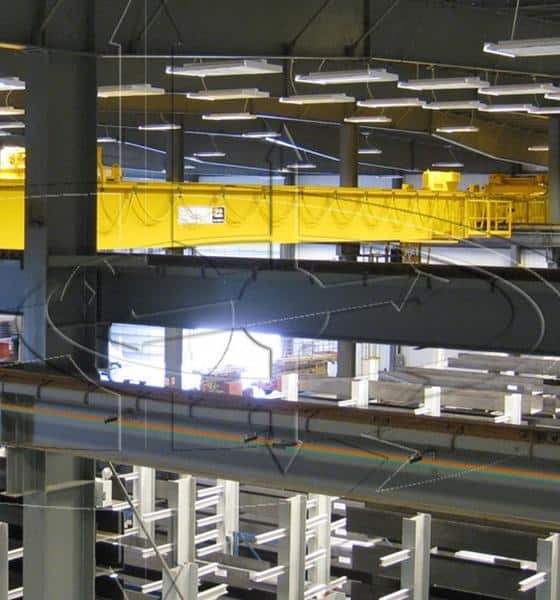