
Crane Anti-Collision Case Study Telemotive …
Crane Anti-Collision Case Study Telemotive Laser Guard Application
Many of you have some knowledge or exposure to anti-collision systems. At Engineered Lifting Systems, we have been engineering and applying Telemotive’s “Laser Guard” systems for anti-collision requirements.

Standard Laser Guard System.
Sure, this system can be used in a conventional application with two outputs that are range adjustable to provide “slow down and stop” or interrupt multiple speed bridge controls to provide “slow down and low speed”. But the system has the flexibility to allow intergraded applications.
We recently applied Laser Guard on two cab operated cranes that the plant engineering and maintenance wanted to make sure did not run into each other at full speed. Historically, cab operated cranes have not used anti-collision in plants, since no one wants to be riding a crane when it runs into another crane! But let’s face it, the operators spend much of their time looking down, and collision in some plants can be a real threat.
This application, however, requires the cranes to work close together often, and as such the typical “slow down and stop” or speed interruption would not work. Using only one Laser Guard, Engineered Lifting Systems developed an interface from two positions (range), and a small PLC to provide outputs. Those outputs are then transferred to the second crane using a standard node (Wi-Fi) radio.

1. Laser Guard head unit
2. Laser Target
3. Laser Guard panel
4. PLC – node panel
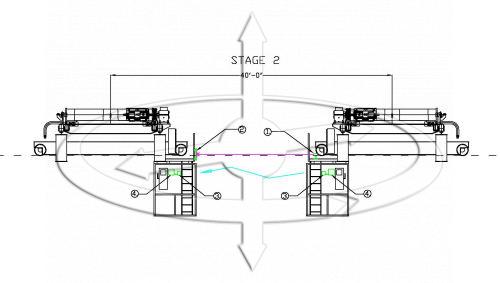
The above illustrations show the two positions that needed to be addressed. In addition to dropping out speed points in the top illustration at 60’, the operator in the cab received an audible and visual indicator that he is within the first zone. Within the 60’ to 40’ distances the operator only has access to the first three speeds in the direction approaching the other crane.
The second illustration shows the second Laser Guard output set at 40’, at which time the brake sets. However, we installed an operator override button that re-sets the anti-collision after the cranes are beyond the 60’ point. This allows the operator to work close to the other crane on the runway as needed, but also keeps the anti-collision in place as needed.


The above picture shows the head unit. This is the PLC/Node panel already dirty after just a mounted in the cab few days, no problem!

This picture shows the visual light in the cab – Green is go!
This application shows the flexibility of the Laser Guard system, and its ability to be part of a dynamic solution for anti-collision.
Before I finish this Newsletter, I would ask that you join with me and welcome Jon Heeley, the newest member of our sales team.

Jon is a very recent mechanical engineer graduating from the University of Missouri Columbia. He is a long time resident of the St. Louis area, plays both ice and roller hockey, and plays golf. We are lucky to have Jon as part of ELS. You may be talking to him when you call in, or email.
As always, if you have a problem with your crane, or just need an idea, please contact Eric Brown @ 866-756-1200 or email ebrown@engineeredlifting.com
Recent news posts
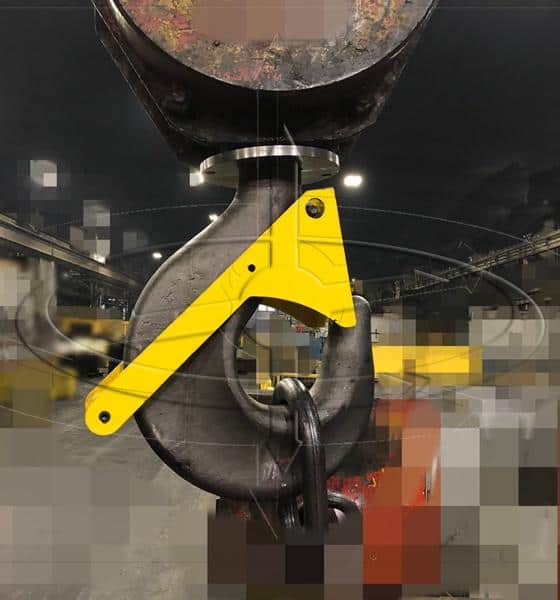
Gravity Latch with Rotation Lock
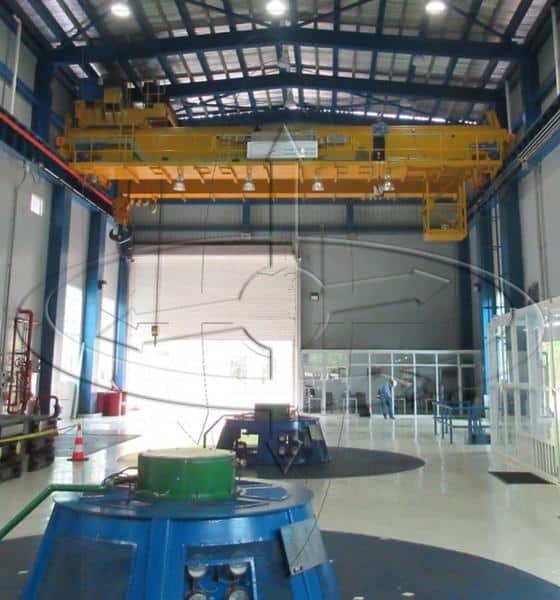
Magnetek Series 3 Drives Using “Motor 2” Option
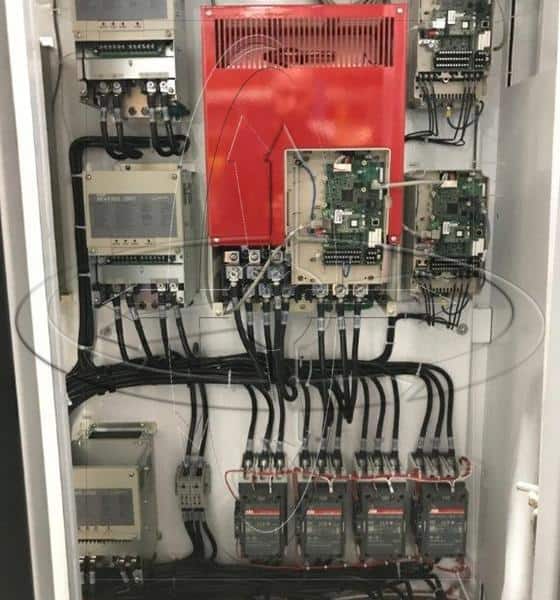
Magnetek Brake Circuit Fusing
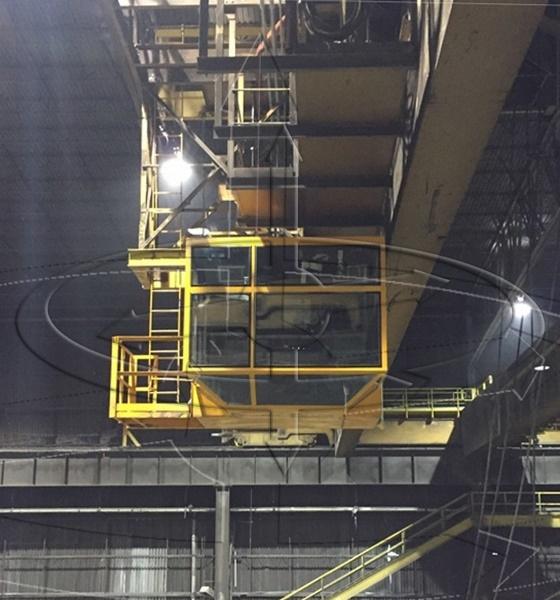
Crane Cab Replacement Improves Function
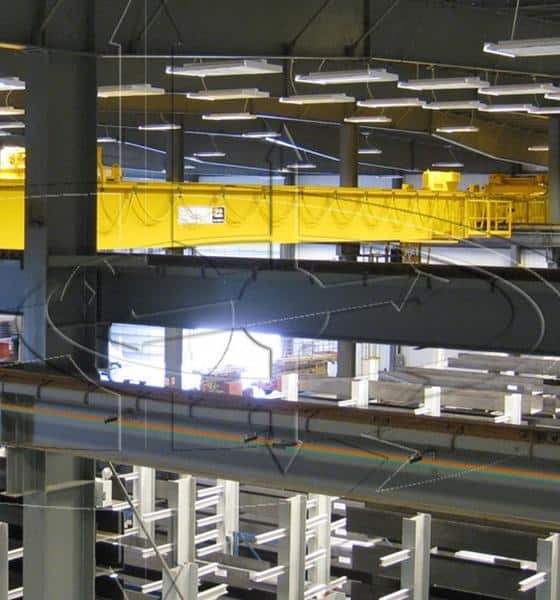